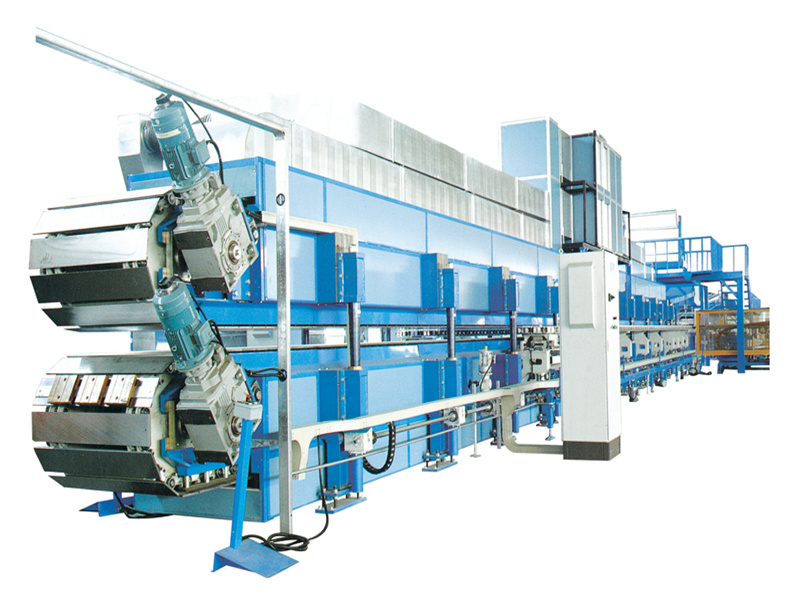
The PU/PIR sandwich panel production line is designed to work with double-sided materials such as pre-painted and galvanized steel, with coil thickness ranging from 0.35 to 0.8 mm, widths up to 1250 mm, and weights up to 10 tons. It accommodates standard coil inner diameters of ø508–610 mm and a maximum outer diameter of ø1300 mm. The core material is rigid foam, either PUR (Polyurethane) or PIR (Polyisocyanurate), compliant with fire classifications B1, B2, or B3. The foam is formed using a precise chemical mixture of polyol, isocyanate, a foaming agent, and a catalyst, with a typical foam density ranging from 35 to 60 kg/m³. These sandwich panels are widely used in applications such as roof panels and cold room construction, offering both thermal insulation and structural support.
TECHNICAL DATA | |
Thickness of board | 30~100mm; 30~150mm; 30~200mm (heavy type) |
Double belt laminator length | 18m; 24m; 36m ;40m |
Maximum opening height | 280mm |
Cover space | L = 90~120m ,W= 20m ,H=6.5m |
Ambient temperature | min. 20℃ ~ max. 60℃ |
Relative air humidity | Average 65 % |
Production speed | 2-12m/minute(Depending upon panel thickness, the property of Polyol & Iso and curing times) |
Total power capacity | About 200KW |
Voltage | 380v/50Hz ±5%( Customized according to the local voltage of the user) |
Frequency | 50Hz(Customized according to the user’s location frequency) |
Voltage of control cabinet | 220V AC |
Compressed air | Volume – 3m3/min (self-provide from local market) |
Sensor voltage | 24v DC |
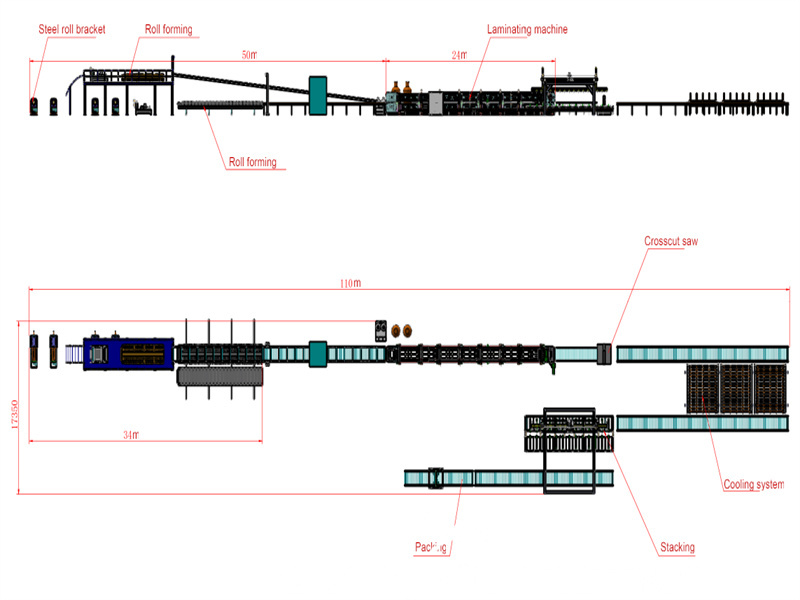
PU-PIR Sandwich Panel Production Machine
Loading car
This lifting car is driven by a hydraulic motor to run the chain wheel, and the chain wheel drives the moving wheel, so that the coil car can move along the guide rail. The lifting device realizes the upper and lower movements through the rod. The lifting stage adopts a tangle pipe, steel mixing welding structure, and a good appearance. The lifting stage can move randomly and stop, and has self –a self-lock protection function
Technical Parameter:
Used for steel coil loading and delivery :10T 2sets
Decoiler speed:0-30m/min (adjustable )
Inner diameter of steel coil:φ508 mm,φ610 mm(Padding block)
Loading material width: Max 1250 mm
Center adjustment: max250mm
Maximum hydraulic pressure: 16 MPa
Hydraulic station motor power: 3 kW
Air pressure: 0.7MPa (factory supplied)
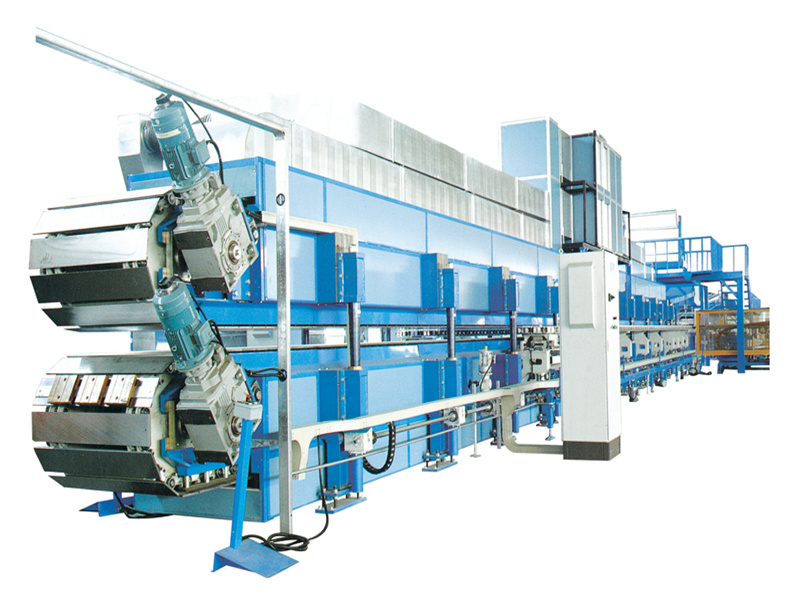
PU-PIR Sandwich Panel Production Machine
Hydraulic Clipper & Film Cover System
This user-friendly unit is a machine tool that performs hydraulic and pneumatic shearing, while also applying protective film to steel sheets. It shares the same hydraulic station as the decoiler.
The clipper uses hydraulic power to cut colored steel sheets and mainly consists of hydraulic cylinders, levers, upper and lower cutting blades, and a robust steel frame.
The film-covering unit includes pneumatic cylinders, gripping rubber rollers, and steel supports. It uses pneumatic force to hold the steel sheet and apply protective film as the sheet is fed through the forming machine. Two film-covering devices are provided—one for the top surface of the sandwich panel and one for the bottom, depending on production requirements.
Additionally, a side trimming function is included to cut away excess board material and ensure the final composite panel meets the required width. This trimming system uses frequency-controlled synchronization to match the line speed. A waste edge rewinding device is also included for collecting trimmed material; it features a modular design for separation and easy mobility within a defined range.
Technical Parameter:
Motor power of broach: 0.75 kW
Speed of broach: about 45 m/min
Motor power of driving roll: 1.5 kW
Speed of driving roll feeding board: about 20m/min
Width of board: Maximum 1250 mm
Thickness of board: 0.35~0.8 mm
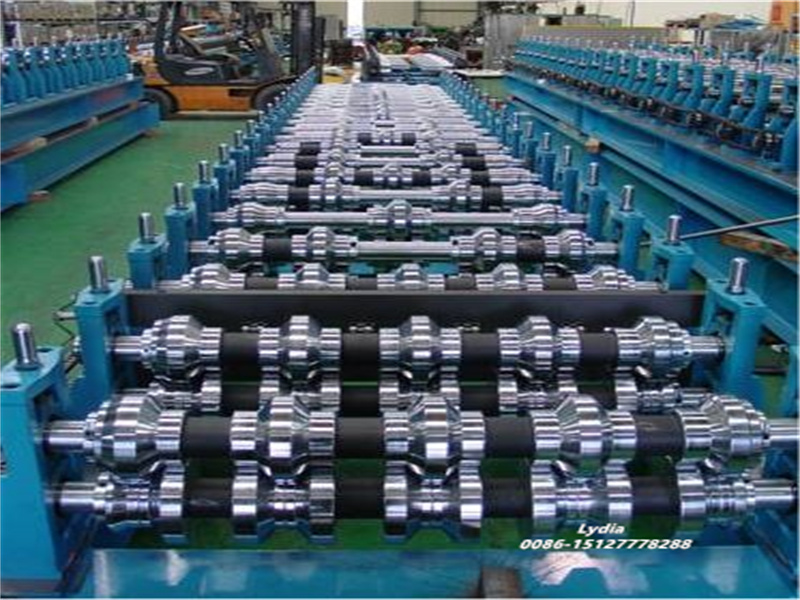
PU-PIR Sandwich Panel Production Machine
1. Forming machine
This machine was installed on a high platform that is used to press and form the inside board of the roof and wall
Specification of color-steel facings for the inside board of the wall and the partition pane
1070mm in width and 0.4~0.6mm in thickness
Forming rollers: 11pairs
Roller diameter: ø50×360L
Maximum forming speed: 8m/min Power: 7.5kw
2. Down forming machine
The down forming machine consists of two forming machines. Adopts the way of the guide rail moving to exchange the profiles. Corrugated plate forming machine, position, and wall panel forming machine can all be replaced. Adopts a rigid connection between machines and is driven by a motor.
Roof plate forming machine for pass shaft type roll forming machine, the width can’t be adjusted.
The bottom sits adopts H-beam welding, giving full consideration to the machine rigidity.
The wall panel forming machine width can be adjusted, the forming roller adopts a single-out shaft cantilever type, and the frame can be adjusted in a certain range. The bottom sits adopts H-beam welding, giving full consideration to the machine rigidity.
3. Roll former moving unit
It is used for a down roll forming machine moving horizontally, which is used for the product change automatically.
Structure: The machine base is suitable for the roll former assembly. The roll forming machine is driven by a motor, and the operator operates it manually. Four rails is suitable for the down roll forming machines moving in a horizontal direction. It will take 5 minutes to change the product. The motor power is 2KW.
◆Cooling system
Sandwich panel will produce a large amount of heat in the process of foaming; it will cause finished panel deformation in the process of stacking if it doesn’t undergo cooling treatment in time. The cooling system is mainly used for keeping finished sandwich panels in “vertical display” under constant temperature conditions. Operation instructions Sandwich panel which has been cut to fixed length be transferred to cooling system sensor—sandwich panel is in preparing state—-panel is away from sensor, roller table stop working—horizontal cylinder be lifted, sandwich panel be transferred into “U” fork—–horizontal cylinder fall, cooling system begin working—–horizontal moving, panel be removed out of “U” fork to be on the rapid roller table—-panel be transferred into stacker |
Technical Parameter:
Length of panel: Max 12000mm Thickness of panel: Max. 200mm Cooling period : 2 Hours Machine dimension: L 15000 mm*12000 mm*2600 mm; Installed power: 10KW; |
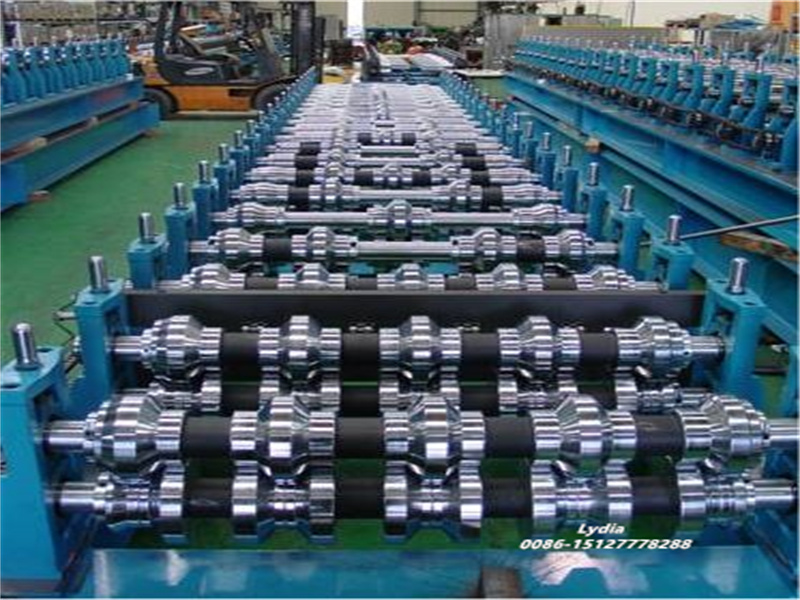
PU-PIR Sandwich Panel Production Machine
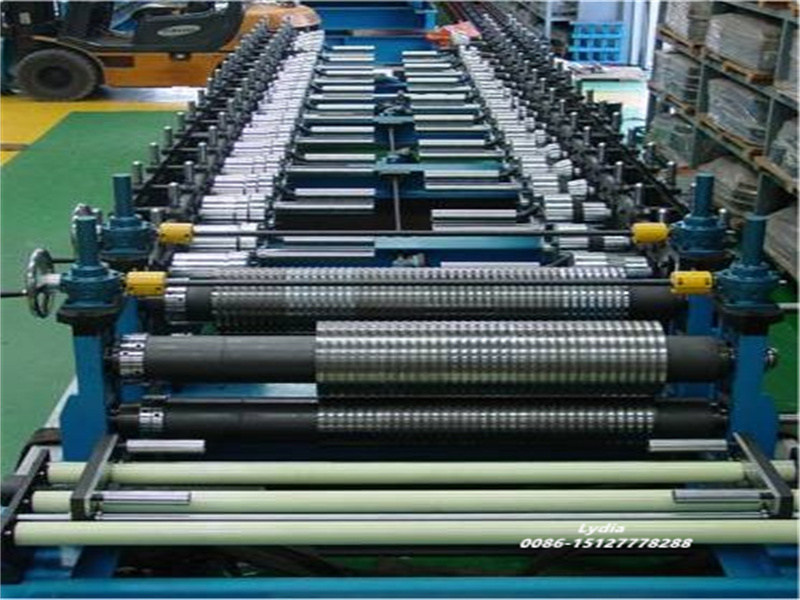
PU-PIR Sandwich Panel Production Machine
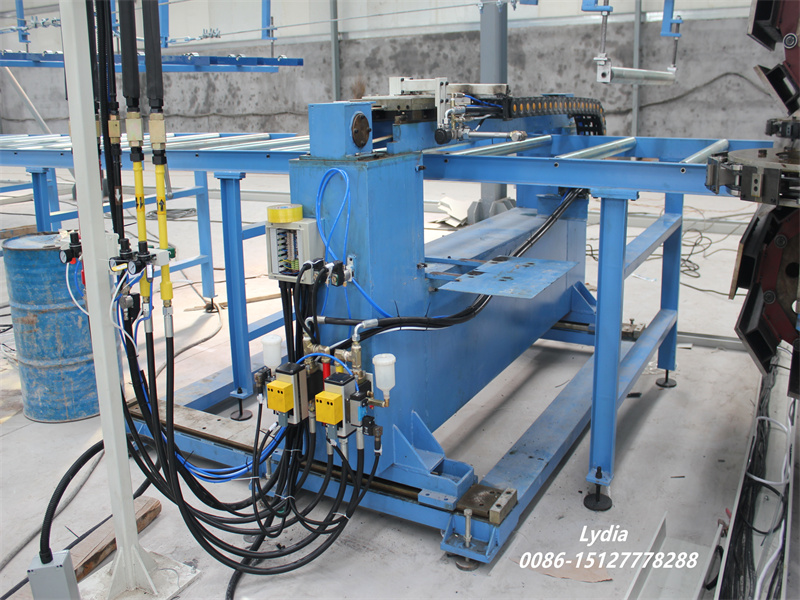
PU-PIR Sandwich Panel Production Machine
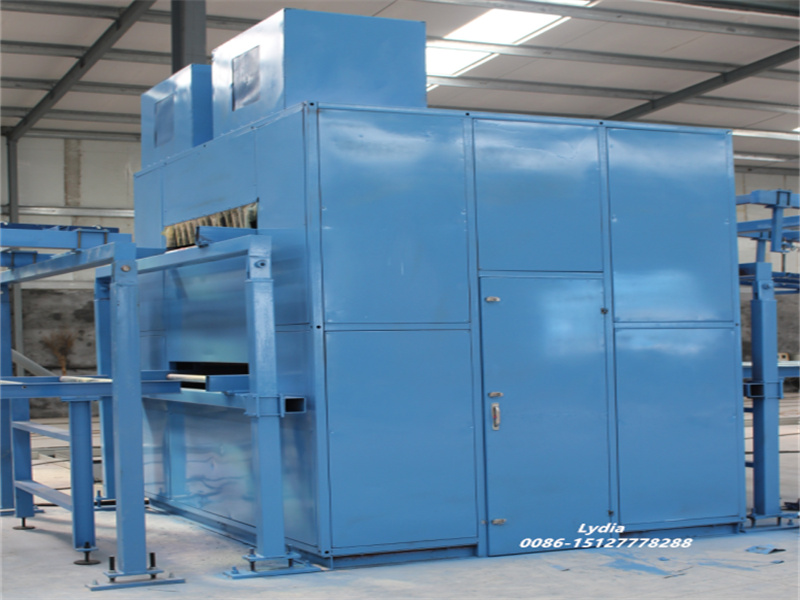
PU-PIR Sandwich Panel Production Machine
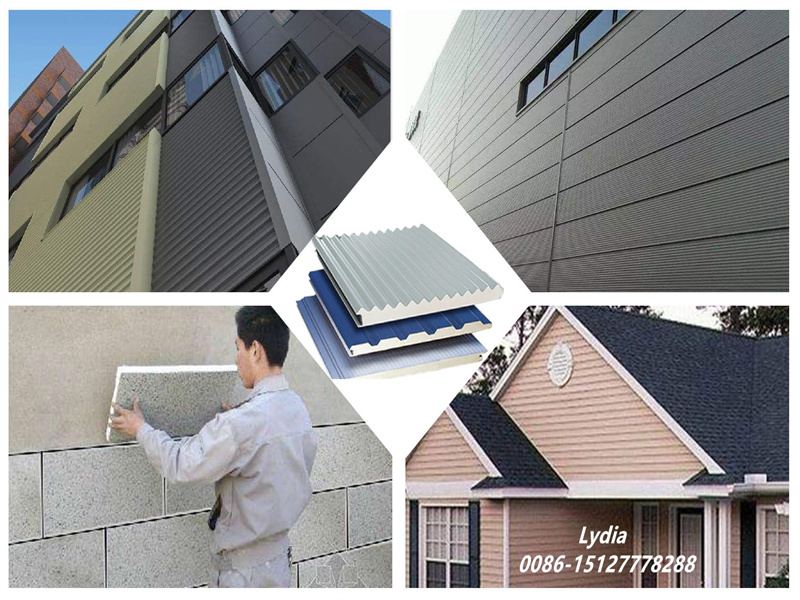
PU-PIR Sandwich Panel Production Machine
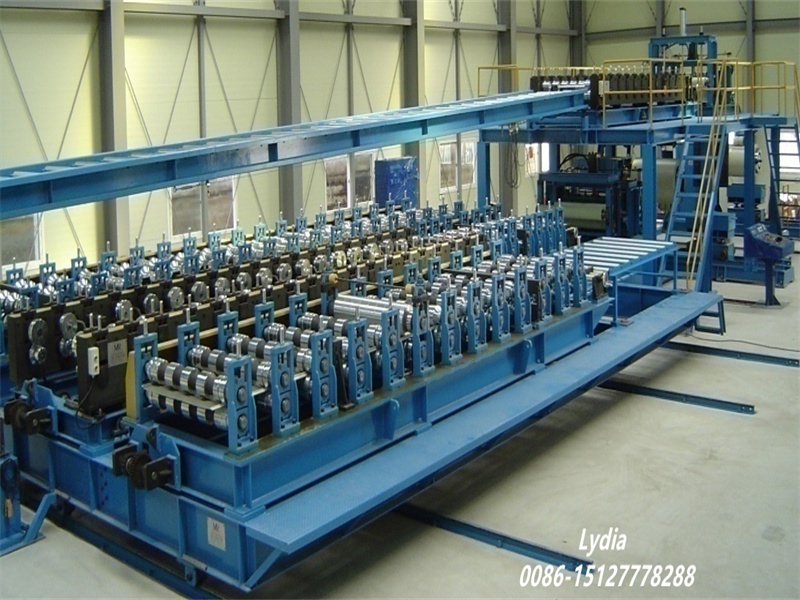
PU-PIR Sandwich Panel Production Machine
Multi-Size Adjustable C U Stud & Track Machines play a vital role in the construction industry by
This roll forming machine is specially designed to produce metal studs, track, furring channel, and
Advantages of the Hydraulic Decoiler 1. The load-bearing spindle is made of high-strength, fatigue-resistant seamless
We are pleased to introduce our advanced slitting line solution, fully prepared for multi-material applications
STAY IN THE LOOP