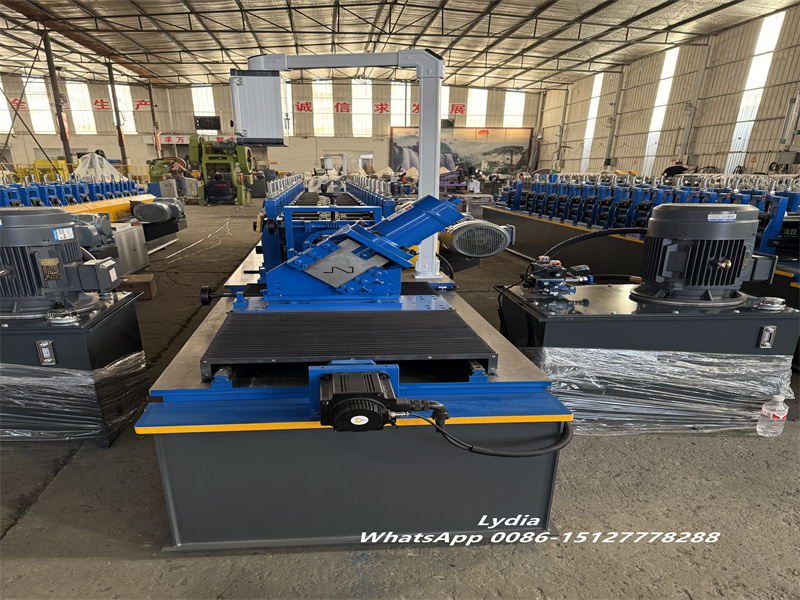
The Z-beam racking system is designed to create a unique, low-profile racking system that maximizes vertical storage efficiency. The system features a Z-beam structure that minimizes rack height while increasing inter-level clearances for more spacious storage.
This racking method stands out for its practicality and high usability with a compact bolt-on construction. The unique Z-beam geometry allows the particleboard platform or shelf to be perfectly flush on top of the beam, eliminating raised edges and creating a clean, streamlined look. The result is a system that combines high load-bearing capacity with aesthetics, making it an ideal choice for cost-effective, light-duty storage applications.
The Z Beam Roll Forming Machine, also referred to as a picking beam roll former, is fully automated and capable of mass-producing Z-type support beams. These beams are often used in racking systems where shelving levels are required for picking and storing loose items. Each Z beam is formed with an integrated four-hook connector at both ends, folded to create a retaining edge that holds the shelving securely in place.
Commonly used in pallet racking systems, Z beams manufactured by this machine help create multiple picking levels efficiently. The Z Beam Boltless Shelving Roll Forming Machine enables reliable and fast production of these profiles, and compatibility with various racking setups.
Z Beam Roll Forming Machine Technical Specification
Item | Specification |
Suitable Material | HCR Coil / Carbon Steel Coil, GI Coil |
Material Thickness | 0.8–2.5 mm |
Profile | 90/100/120*70 mm |
Line Speed | 20 m/min |
Production Flow
Steel Coil → Straightening Machine → Punching Machine → Roll Forming Machine → Hydraulic Cut Off → Run Out Table → Finished Product → PLC Control
Decoiler
Category | Item | Specification |
Decoiler | Coil Outer Diameter | Max. 1600 mm |
Coil Inner Diameter | 460 – 520 mm | |
Coil Width | 500 mm | |
Coil Weight | Max. 3000 kg | |
Tensioning Method | Manual with Manual Brake | |
Special Feature | With Anti-Uncoil Frame | |
Leveling Machine | Material Width | 400 mm |
Material Thickness | Up to 2.5 mm | |
Rollers | 11 pcs (GCr15 steel, HRC55–57°) | |
Transmission | Chain and Gear | |
Motor Power | 3 kW | |
Material Feeder | Feeding Width | 400 mm |
Feeding Thickness | 2.5 mm | |
Rollers | 4 pcs (GCr15, HRC55–57°) | |
Servo Motor | 1.8 kW | |
Transmission | Gear-driven | |
Power Press | Punching Pressure | 80 Tons (Air Clutch) |
Punching Frequency | Up to 60 times/min | |
Punching Moulds | 3 sets (90 mm, 100 mm, 120 mm) | |
Main Roll Forming | Material Thickness | 1.8 – 2.5 mm |
Adjust Width | By spacer | |
Roller Stations | 24 groups | |
Straightening Rollers | 5 pcs | |
Roller Material | GCr15, HRC55–57°, polished | |
Main Shaft Diameter | 60 mm (45# steel) | |
Bearings | 60310 series | |
Wall Plate Thickness | 30 mm | |
Drive Mode | Gear and Chain | |
Drive Motors | 3 sets of 5 kW | |
Cooling System | Water Cooling Equipped | |
Hydraulic Cut-Off | Hydraulic Station | 1 set |
Motor Power | 4 kW | |
Cutting Moulds | 4 sets | |
Blade Material | SKD11 (HRC60–62°) | |
Cutting Mode | Stop-to-Cut | |
Run-Out Table | Length | 6 meters |
Structure | Welded Angle Steel | |
Discharge Type | Pneumatic | |
Control System | Controller | PLC with Touchscreen |
Length Control | Encoder-based | |
Speed Control | Transducer (Inverter) | |
Electrical Components | High-quality branded parts | |
Power Supply | Customized as required |
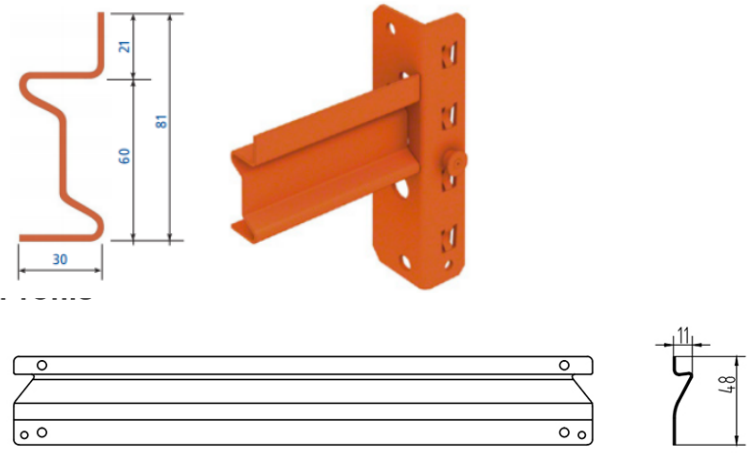
Z-beam Roll Forming Machine
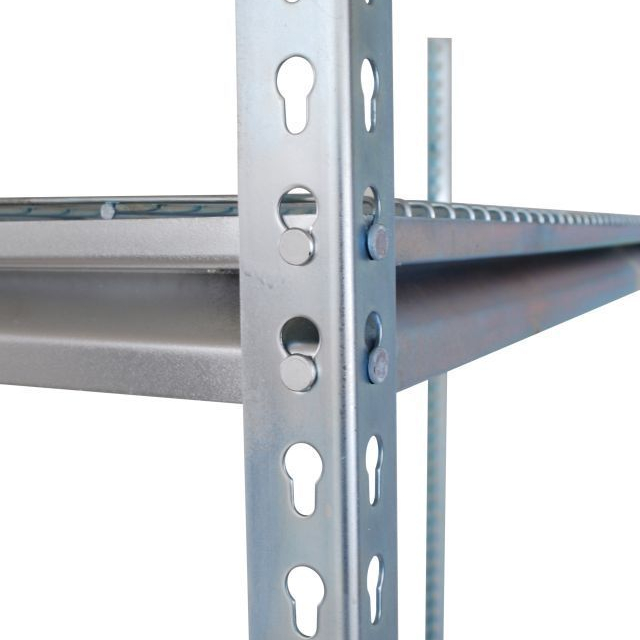
Z-beam Roll Forming Machine
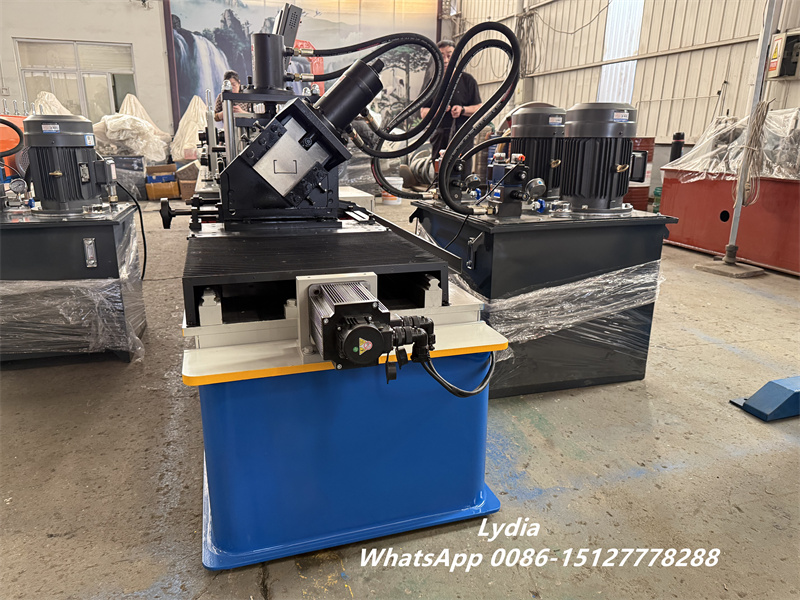
Z-beam Roll Forming Machine
Modern construction projects demand highly efficient and precise equipment to produce structural components such as
Aluminum Corner Roll Forming Machine The Aluminum Corner Roll Forming Machine is a precision-engineered production
This automated production line represents a significant advancement in light steel framing technology. Designed specifically
Hydraulic Press Brake 350T3200 with TP10S CNC System, High-Precision Torsion Bar Bending Machine We are
STAY IN THE LOOP