
Zhongtuo’s roll-forming machines stand out through a clear emphasis on precision, durability, and thoughtful engineering—offering reinforced structures, advanced control systems, and superior component design. Compared to typical competitors, Zhongtuo delivers longer machine life, higher production accuracy, and easier maintenance, making them a reliable choice for demanding industrial applications.
**Zhongtuo** uses a rotating wheel plus a brake: stable unwinding and prevention of coil buildup on the floor.
**Others** often lack braking, so material can overshoot and tangle.
**Zhongtuo** multiple support rollers, adjustable hand wheels, nylon trays, pinch rollers, and manual cutters—resulting in gentle, accurate, damage‑free feeding.(Advantages:
- With several support rollers, to feed the material more stable, protect the steel coil without curl up
- With hand wheels to adjust the feeding size, more convenientlyto make the feeding width fit the material width.
- Equipped with 2 nylon tray in the middle of the platform and two sets of pinch rollerto feed the material, prevent the material surface from being damaged, and feed the material more easily and quickly
- Top layer and bottom layer with manual cutter to cut the feed material more easily.)
**Others** typically use fewer rollers, no trays or dedicated cutters, risking coil damage and slower setup.
- **Zhongtuo**:four‑column frame (40Cr steel), dual‐row bolt fixation and steel bar clamp, top sheet insertion—yields far greater rigidity, blade life, and cut precision.
- **Others**:two columns and single‐screw mounting, prone to vibration, looseness and early wear.
Our other advantages
- **Zhongtuo**: heavy‑duty cylinder with fine‑machined, galvanized oil tubing—smoother flow, higher service life.
- **Others**:lighter, less‑refined components, shorter lifespan.
- **Zhongtuo**: genuine Ø80 mm rollers, H‑frame ≥ 350 mm, thicker wall plates (18–20 mm), through‑hard‑chrome, dual CNC grindings, bearings—ensures hardness, precision, long life, no paint scuffing.
- **Others**: undersized or thin rollers/frames, thin chrome, limited machining, no bearings—more scratches, wear, and inaccuracy.All of these affect the machine producing cost, also affect the machine weight. For our double layer machine, around 9-10 ton. But many factories, machine is around 7 tons.
- **Zhongtuo**:air‑cooled tank with fan, larger pipes and valves—keeps oil temperature down during long runs and supplies ample power.
- **Others**: smaller pumps, no cooling, undersized tubing/valves—risk overheating and under‑powering.
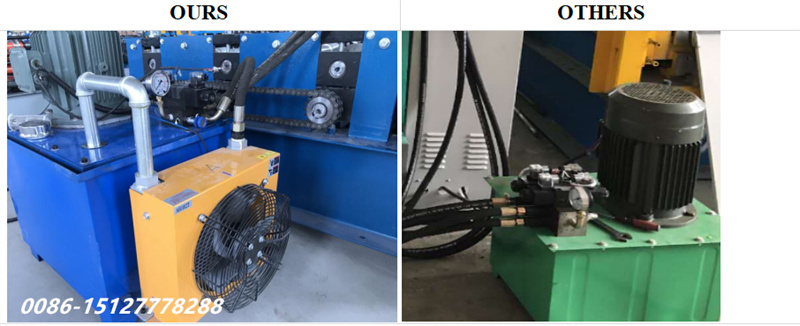
Roll Forming Machine
- **Zhongtuo**: insert design with cushioning under bolts, seamless 2–3 mm pipes, anti‑loosen slots and double gears—prevents shafts or spacers from coming loose, ensures dimensional accuracy and easy maintenance.
- **Others**: direct bolt mounting, small seams, no cushions—shafts loosen over time, spacers deform, sheets lose precision, repairs difficult.
- **Zhongtuo**: dual chains for efficiency and a clutch device—allows upper or lower layer to run independently, saving power and reducing wear.
- **Others**: simple linkage—both layers always turn together, higher energy use and stress.
- **Zhongtuo**:aviation‑plug connectors; spacious, well‑ventilated cabinet; major‑brand PLC/inverter (Siemens, Schneider); touchscreen; fully labeled wiring; strategic Siemens partnership.
- **Others**:cramped boxes, non‑branded components, minimal labeling, no cooling—harder installation, maintenance and prone to overheating.
Cangzhou, China – Zhongtuo Cold Forming’s Global Industry Procurement Center has become a bustling hub
Zhongtuo’s Floor Deck Machines Revolutionize Mexican Construction with Smart Manufacturing Monterrey, Mexico – Zhongtuo Cold Forming
At the beginning of July, Zhongtuo Cold Bending Technology welcomed a wave of “hot” customers
Good News-Zhongtuo successfully commissioned a fully automatic punching line for an Italian customer
July 2025 – Botou, Hebei, China Zhongtuo Roll Forming Machinery Co., Ltd. announced that the
STAY IN THE LOOP