
Ridge Cap Roll Forming Machine Advanced Structural Configuration
This precision-engineered system integrates 18 sets of chromium-plated rollers (#45 steel, HRC55-60°) with PLC-controlled automation, ensuring dimensional accuracy within ±2mm tolerance. The modular design accommodates various roofing profiles while maintaining production speeds up to 10m/min.
Advantages of Glazed Tile And Ridge Cap Roll Forming Machine
1. Finished Tile Profile – Edge Design
Many manufacturers use a wavy edge design at the bottom edge of the tile, which leads to poor overlap and loose joints. Our finished tile has a very straight and flat edge, resulting in a strong three-dimensional appearance and tight, seamless overlap.
2. Forming Method – Split Forming System
We adopt a split forming structure to ensure that every edge of the tile remains straight and flat, avoiding any waviness, imprinting, or indentation. This method provides greater stability during continuous high-speed operation.
3. Automatic Lubrication System
Manual maintenance often falls behind, causing guide rails to dry out and cutting dies to wear, leading to machine downtime. Our solution includes an automatic oiling system and additional supporting rollers to ensure smooth material feeding and to avoid blade impact.
4. Molding and Cutting Sequence
* If both the front and back ends of the tile are arc-shaped, it indicates post-forming cutting (cutting after roll forming).
* If the front is arc-shaped and the back is flat, it indicates pre-punch cutting (cutting before roll forming).
These differences reflect the production process designs specific to glazed tile and ridge cap roll forming machines.
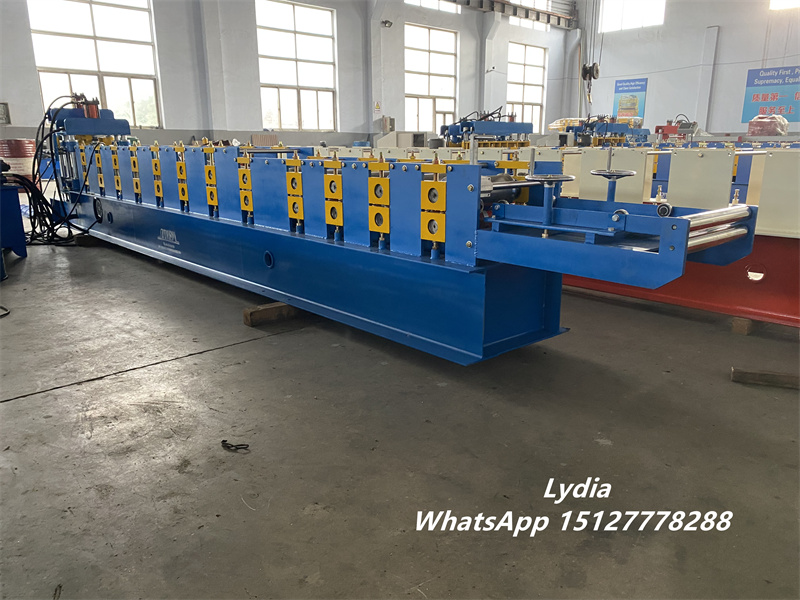
Glazed tile and ridge cap roll former
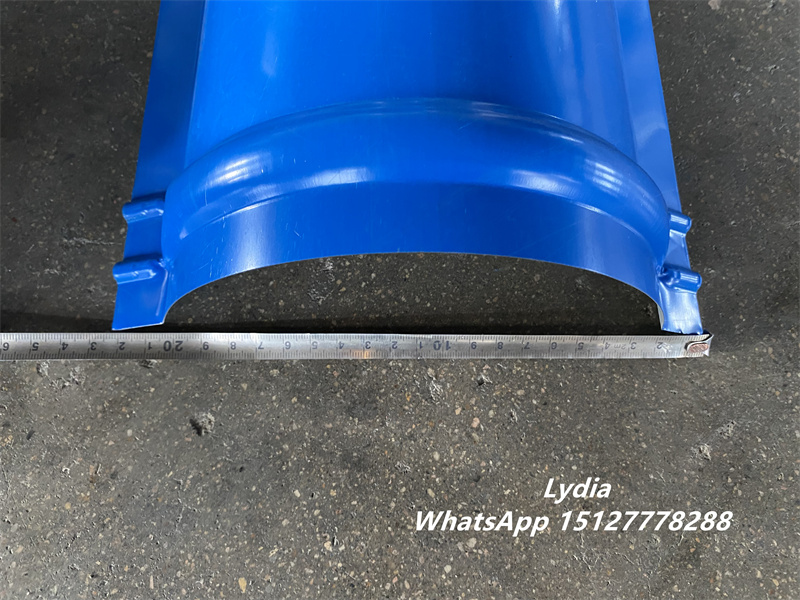
Glazed tile and ridge cap roll former
Material Compatibility in Ridge Cap Roll Forming Machine Applications
Specially calibrated for processing 0.4-0.8mm thickness materials including PPGI, galvanized steel, and aluminum alloys. The hydraulic decoiler system handles coils up to 1200mm diameter with 3000kg loading capacity, compatible with coil widths from 300mm to 550mm.
Ridge Cap Roll Forming Machine Production Workflow Optimization
1. Automated coil feeding with directional guidance
2. Multi-stage progressive forming through 18 roller stations
3. Programmable length determination via omron encoder
4. Hydraulic punching and precision cutting (CR12 steel blades)
5. Output conveyance with protective film application
Energy-Efficient Operation of Ridge Cap Roll Forming Machines
Equipped with 4KW servo motors and chain transmission mechanisms, the system reduces power consumption by 25% compared to conventional models. The touchscreen HMI (Delta PLC) supports multi-language operation, including real-time production monitoring and error diagnostics.
Quality Assurance Protocols for Ridge Cap Roll Forming Machine Output
Implementation of ISO 9001-certified inspection procedures ensures:
– Consistent profile geometry verification
– Surface finish evaluation (salt spray test compliant)
– Load-bearing capacity certification (up to 1500N/m)
– Interlock seam integrity testing
Modern construction projects demand highly efficient and precise equipment to produce structural components such as
Aluminum Corner Roll Forming Machine The Aluminum Corner Roll Forming Machine is a precision-engineered production
This automated production line represents a significant advancement in light steel framing technology. Designed specifically
Hydraulic Press Brake 350T3200 with TP10S CNC System, High-Precision Torsion Bar Bending Machine We are
STAY IN THE LOOP