Technical Parameters for Angle Steel Cold Roll Forming Production Line
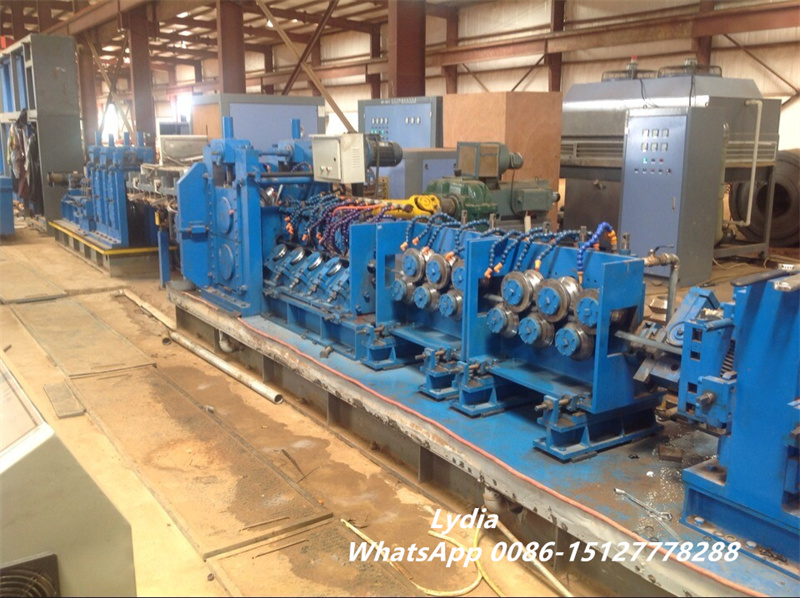
Angle Iron Steel Roll Forming Machine
I. Summary
The ZTRFM Angle Steel Cold Roll Forming Production Line is an economical and innovative profile steel production line developed by our company. Using roll bending deformation combined with hot rolling, it can process low carbon or low alloy steel strips into a variety of angle steel profiles. The outer fillets of the produced angles are sharp, and the sectional dimensions meet national hot-rolled angle steel standards. Its surface quality and performance exceed those of traditionally hot-rolled equivalents.
Material: HR steel coil, (δb≤ 500MPa, δs≤ 235MPa)
II. Technical Flow
{SteelTape} → Single-arbor uncoiler → Strip-head Cutter & Welder → Cage Loop → Feeding → Pre-forming → Induction Heating → Squeeze Upsetting → Finishing Molding → Polishing & Blunt → Cooling & Straightening → Speed Testing → Drawing Stand → Twist Adjustment → Computer Controlled Cutting Saw → Run-out Table → Blanking & Packaging
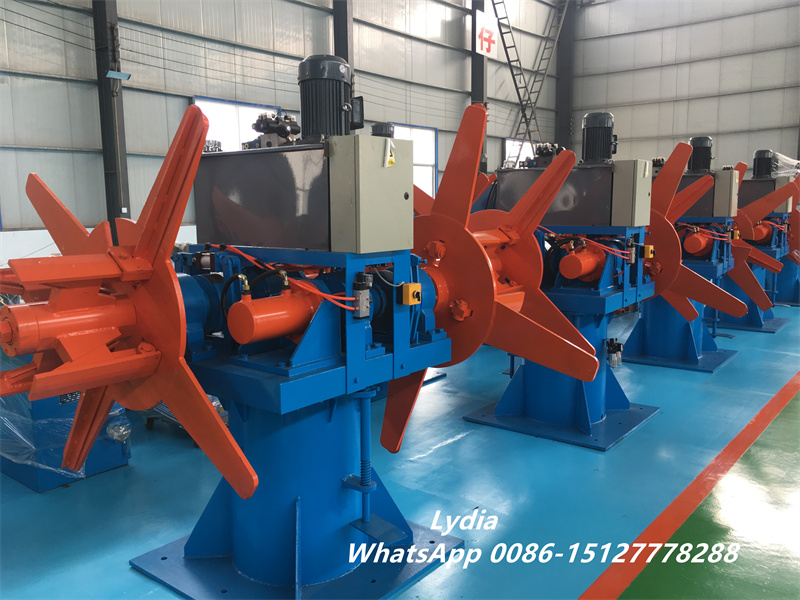
Angle Iron Steel Roll Forming Machine
III. Basic Conditions
- a) Product Specifications
Angle Steel Side Length | 20×20, 25×25, 30×30, 36×36, 40×40, 45×45, 50×50 mm |
Thickness | 1.5 – 3.5 mm |
Cutting Length | 4 – 6 m |
Material | HR Carbon Steel Coil, (δb≤500Mpa, δs≤235Mpa) |
- b) Steel Material Specification
Strip Width | 40 mm – 100 mm |
Strip Thickness | 1.5 mm – 3.5 mm |
Inner Diameter | Φ470 – 510 mm |
Outer Diameter | Φmax = 1800 mm |
Max Weight | 4.0 tons |
- c) Other Parameters
Line Speed | 20 – 70 m/min |
Installed Power | Approx. 1000 KW |
Line Dimensions | Approx. 60 x 6 m |
1.1. Application: it is used to support the steel coil and open up the coil to strip, preparing for the next process.
1.2. Structure: Double-arbor hydraulic uncoiler.
1.3. Parameters:
Inner diameter: Φ470-510mm
Outer diameter: Φmax=1800mm
Strip steel width: 40mm-100mm
Strip steel thickness: 1.5mm-3.5mm
The maximum weight: 2.0 tons
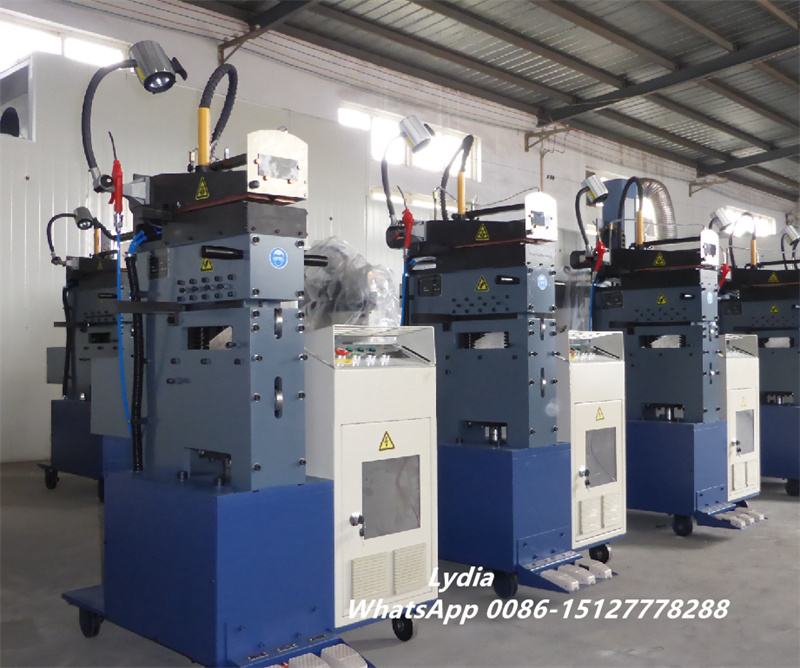
Angle Iron Steel Roll Forming Machine
- Shearing & butt welding machine
2.1. Application: It is used to parallel cut the trail of the strip, which has just gone into the accumulator, and the head of the strip coming out of the uncoiler, and then weld them together, to maintain a continuous production.
2.2. Structure: Cutting by hydraulic, welding by automatic
Strip steel thickness: 1.5-3.5mm
Strip steel width: 40-100mm
3.1. Application: is used to receive strip steel discontinuously from the uncoiler and at the same time provide the steel strip to the forming unit continuously.
3.2. Structure: cage loop, contains two part: pinch machine and cage body.
Cage body length: 6m, height: 2.5m
Strip steel thickness: 1.5-3.5mm
Strip steel width: 40-100mm
Storage length: 300-400m
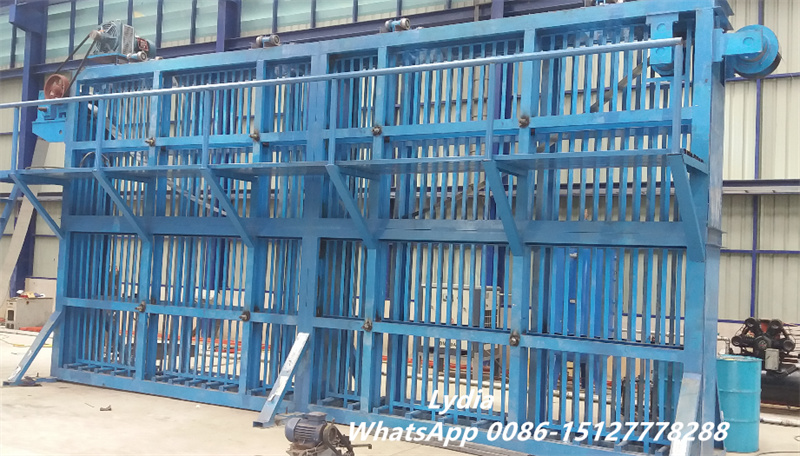
Angle Iron Steel Roll Forming Machine
- Feeding unit
4.1. Application: It is used to deliver the steel strip to the forming machine smoothly, and rectify the steel strip’s bending defect at the same time.
4.2. Structure: Composed of two sets of vertical rollers and one set of a Five-roll passive leveling machine. A set of flat roller is installed before the first vertical roller; it can reduce the steel strip’s beating amplitude in the running, ensuring the smooth production.
- Pre-forming stand
5.1. Application: fold the steel by roll forming into a certain angle billet.
5.2. Structure: Gantry arch structure. The down roller is driving rotation through the motor reducer, threading, and feeding. The shaft is equipped with a pneumatic clutch, disengaged by power in production. The upper roller is a passive roller, its movements is using a worm structure, and electric synchronous adjustment.
Forming unit: 2 sets
Forming shaft diameter: Φ150mm material: 42CrMo
high-frequency quenching
- Squeezing and Pier-coarse machine
7.1. Application: Extruding the angle billet after heat treatment, make the angle steel corner’s material accumulation, to stay out of material margin and deformation margin for the further corner sharp rolling.
7.2. Structure: using the three-roller extruding form. It can easily realize the opening-closing extrusion adjustment, and lifting adjustment in the operation side. Drawing plate is equipped on the vertical roller shaft, to control the deformation amount of the roller easily.
Shaft diameter: Φ80mm material: 42CrMo
high-frequency quenching.
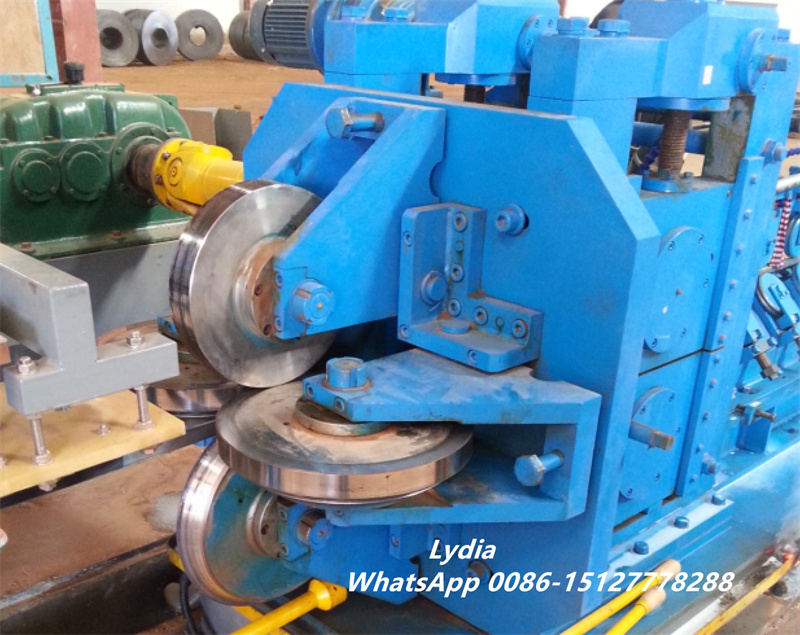
Angle Iron Steel Roll Forming Machine
- Finishing machine
8.1. Application: Roll forming the angle billet into finished steel angle basic outer dimensions.
8.2. Structure: Gantry arch structure. The down roller is actively rotating through
the motor reducer, when working, the preformed stand motor clutch disengaged, the angle billet is drawing by finishing machine. The upper roller lifting uses the worm gear structure, electric adjustment.
Finishing shaft diameter: Φ150mm material: 42CrMo
high-frequency quenching
- Polishing blunt stand
9.1. Application: through two sets of vertical rolls and upper pressuring roller, the stand makes the outside of Angle steel edge polishing and blunt.
9.2. Structure: Six sets of vertical rollers and upper roller stand make up as Three-roll blunt pass. Vertical roll can be opening- closing and lifting adjusted. The upper roller can be lifting adjusted, and the axial can be translation adjusted. So that the rolling line centre position is convenient to adjust. Rollers can be shared.
Roller diameter: Φ80mm material: 42CrMo
high-frequency quenching
- Cooling table
Length: 15m
- Water Cooling device
Length: 2.0m
- Drawing stand
12.1. Application: provide the supplementary motivation of the angle steel advancing.
12.2. Structure: same to the performed stand, the power system and finishing machine centralized driving, ensure the production line speed matching.
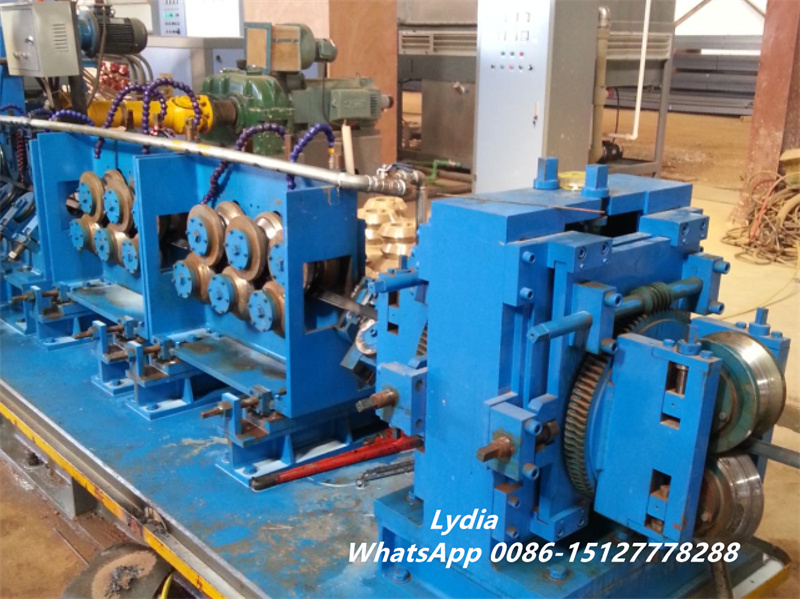
Angle Iron Steel Roll Forming Machine
Modern construction projects demand highly efficient and precise equipment to produce structural components such as
Aluminum Corner Roll Forming Machine The Aluminum Corner Roll Forming Machine is a precision-engineered production
This automated production line represents a significant advancement in light steel framing technology. Designed specifically
Hydraulic Press Brake 350T3200 with TP10S CNC System, High-Precision Torsion Bar Bending Machine We are
STAY IN THE LOOP