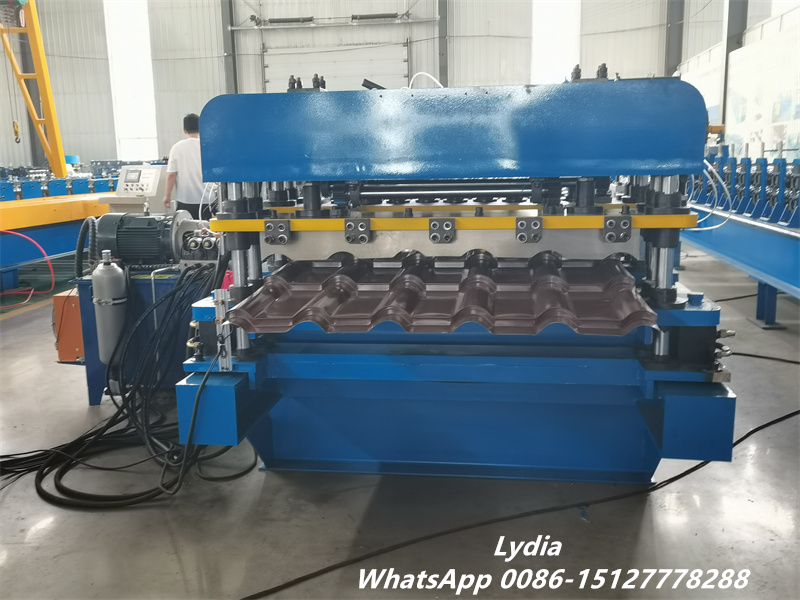
Glazed Tile Roll Forming Machine for Step Roof Panels – Enhanced Overview
Glazed tile roll forming machines are specialized equipment designed to produce step-style metal roof tiles from high-quality pre-painted steel coils. These elegant metal tiles are especially favored for roofing in villas and upscale residential constructions, where both visual appeal and structural performance are required.
What sets these tiles apart from standard roof panels is the stepped pattern across the surface. A conventional metal roofing sheet becomes a glazed tile once step embossing is applied. Unlike standard panel forming machines, this type of equipment integrates a hydraulic step-pressing mechanism, which adds dimensional steps to the pre-formed sheets, offering a classic tiled appearance with modern material strength.
Structural Features and Capabilities Roof Glazed Tile Roll Forming Machine
Not every roofing panel profile is compatible with step pressing. Only select designs can be processed through this system, which often results in a machine that is more complex and specialized than a typical roof panel roll former. A glazed tile machine typically includes more roller stations, higher structural rigidity, and precise control over step depth and pitch, thanks to the dedicated hydraulic press.
These machines generally consist of:
Manual or optional hydraulic decoiler
- Feeding guide and film protection system
- Precision roll forming unit
- Hydraulic press for step formation
- Hydraulic cutter
- Programmable logic control (PLC) unit
- Run-out tables for panel collection
The step pressing device is strategically positioned between the roll forming station and the cutting unit. Operators can easily adjust step height, length, and count using the touchscreen interface on the PLC control system—allowing full customization for various project needs.
Technical Specifications Summary
Item | Details |
Raw Material | Pre-painted/color-coated steel coils |
Thickness Range | 0.3 mm – 0.6 mm |
Coil Width | 1000 – 1250 mm |
Roll Stations | 16–25 stations (based on profile complexity) |
Roller Material | 45# steel with hard chrome plating |
Roller Shaft Diameter | 70–80 mm |
Decoiler Type | Manual or hydraulic (optional) |
Main Motor Power | 5.5 – 7 kW |
Hydraulic Power | 5.5 kW |
Pressing/Shearing Die | Cr12 steel with heat treatment |
Forming Speed | 0–15 m/min (approx. 20 steps/min) |
Cutting Precision | ±1.5 mm |
Control System | Panasonic PLC + Touchscreen |
Power Requirement | 380V / 50Hz / 3 Phase |
Machine Dimensions (L×W×H) | Approx. 8500 × 1500 × 1200 mm |
Total Weight | Approx. 6–8 tons |
Modern construction projects demand highly efficient and precise equipment to produce structural components such as
Aluminum Corner Roll Forming Machine The Aluminum Corner Roll Forming Machine is a precision-engineered production
Cangzhou, China – Zhongtuo Cold Forming’s Global Industry Procurement Center has become a bustling hub
This automated production line represents a significant advancement in light steel framing technology. Designed specifically
STAY IN THE LOOP